6000 Series Aluminum Alloy
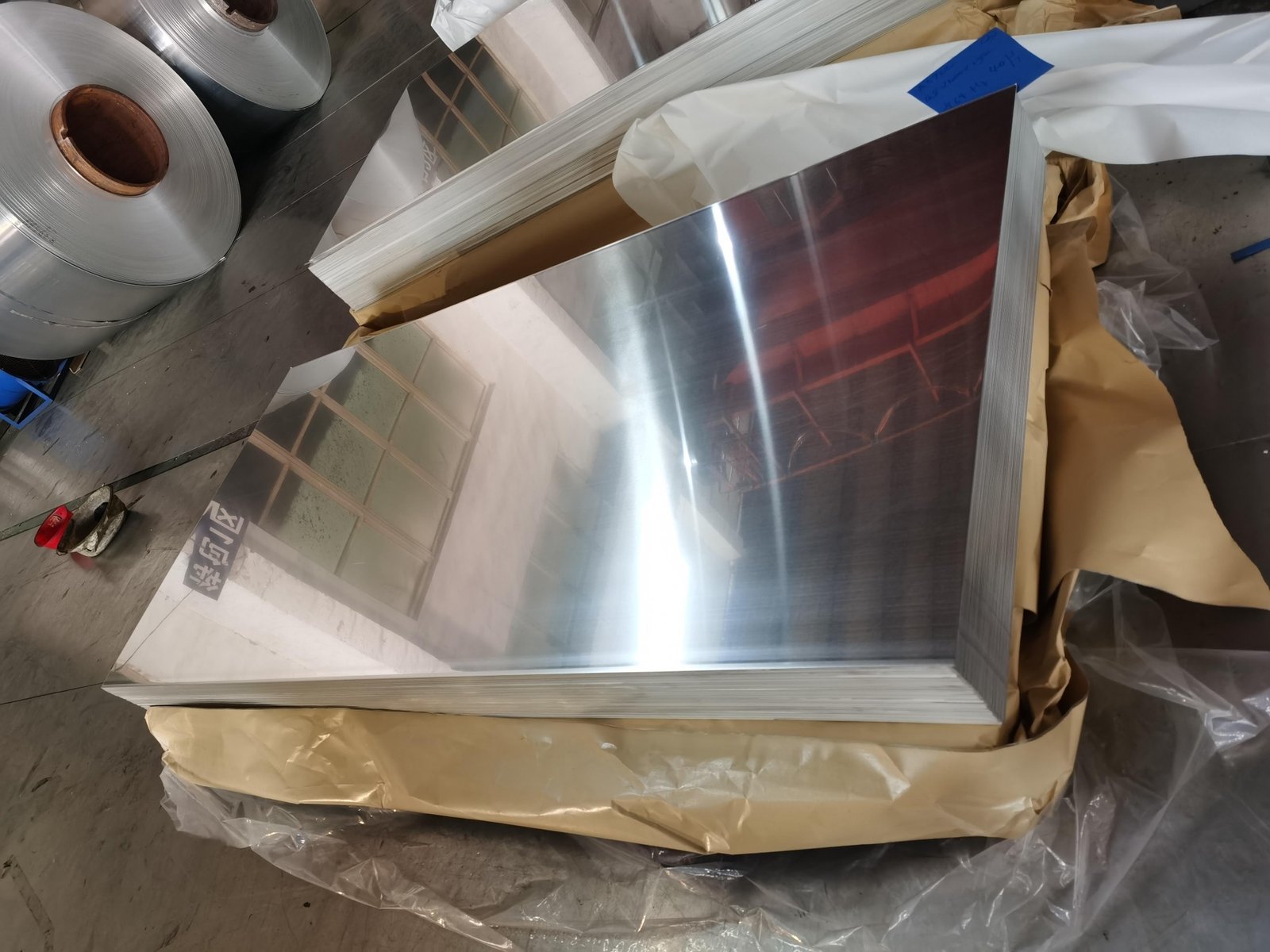
The 6000 series aluminum alloy, renowned for its balance of strength, formability, and corrosion resistance, has become a cornerstone material in industries ranging from aerospace to construction. Combining magnesium and silicon as primary alloying elements, these alloys offer versatility that meets the demands of modern engineering. In this article, we delve into the composition, key characteristics, applications, and future trends of 6000 series aluminum alloys.
What Is 6000 Series Aluminum Alloy?
The 6000 series (Al-Mg-Si alloys) is a group of heat-treatable aluminum alloys primarily composed of magnesium (Mg) and silicon (Si). These elements form magnesium silicide (Mg₂Si) during heat treatment, enhancing mechanical properties such as tensile strength and hardness. Common grades include:
- 6061: The most widely used, known for excellent weldability and structural integrity.
- 6063: Favored for extruded profiles due to superior surface finish.
- 6082: Offers higher strength, ideal for load-bearing components.
Key Properties of 6000 Series Aluminum
-
High Strength-to-Weight Ratio
Heat treatment (T4, T6 tempering) significantly boosts strength, making these alloys comparable to mild steel but 65% lighter. -
Corrosion Resistance
A natural oxide layer protects against environmental degradation, suitable for marine and outdoor applications. -
Machinability and Formability
Easily extruded, welded, and anodized, 6000 series alloys adapt to complex shapes without sacrificing performance. -
Sustainability
Fully recyclable, aligning with global green manufacturing initiatives.
Applications Across Industries
The versatility of 6000 series aluminum alloys drives their use in:
- Automotive: Engine components, chassis, and lightweight body panels (e.g., Tesla and BMW electric vehicles).
- Construction: Window frames, roofing, and structural supports (e.g., the Burj Khalifa’s curtain walls).
- Aerospace: Wing sections and fuselage parts requiring fatigue resistance.
- Consumer Electronics: Smartphone frames and laptop casings for durability and aesthetics.
Processing and Fabrication Tips
- Heat Treatment: Solution heat treatment followed by quenching and aging maximizes strength.
- Extrusion: 6063’s low deformation resistance makes it ideal for intricate cross-sectional profiles.
- Welding: Use TIG or MIG methods; avoid overheating to prevent strength loss.
Market Trends and Future Outlook
With the push toward lightweighting in transportation (EVs) and energy-efficient buildings, demand for 6000 series alloys is projected to grow at a CAGR of 5.2% through 2030. Innovations in nano-coatings and hybrid alloy development (e.g., Al-Mg-Si-Cu) aim to further enhance wear resistance and thermal stability.
Conclusion
6000 series aluminum alloys exemplify the synergy of engineering and material science, offering unmatched adaptability for modern challenges. Whether optimizing vehicle efficiency or constructing resilient infrastructure, these alloys remain a go-to solution. For manufacturers and designers, understanding their properties and applications is key to unlocking next-generation innovations.