From Design to Production: The Process Behind Manufacturing Tin Boxes
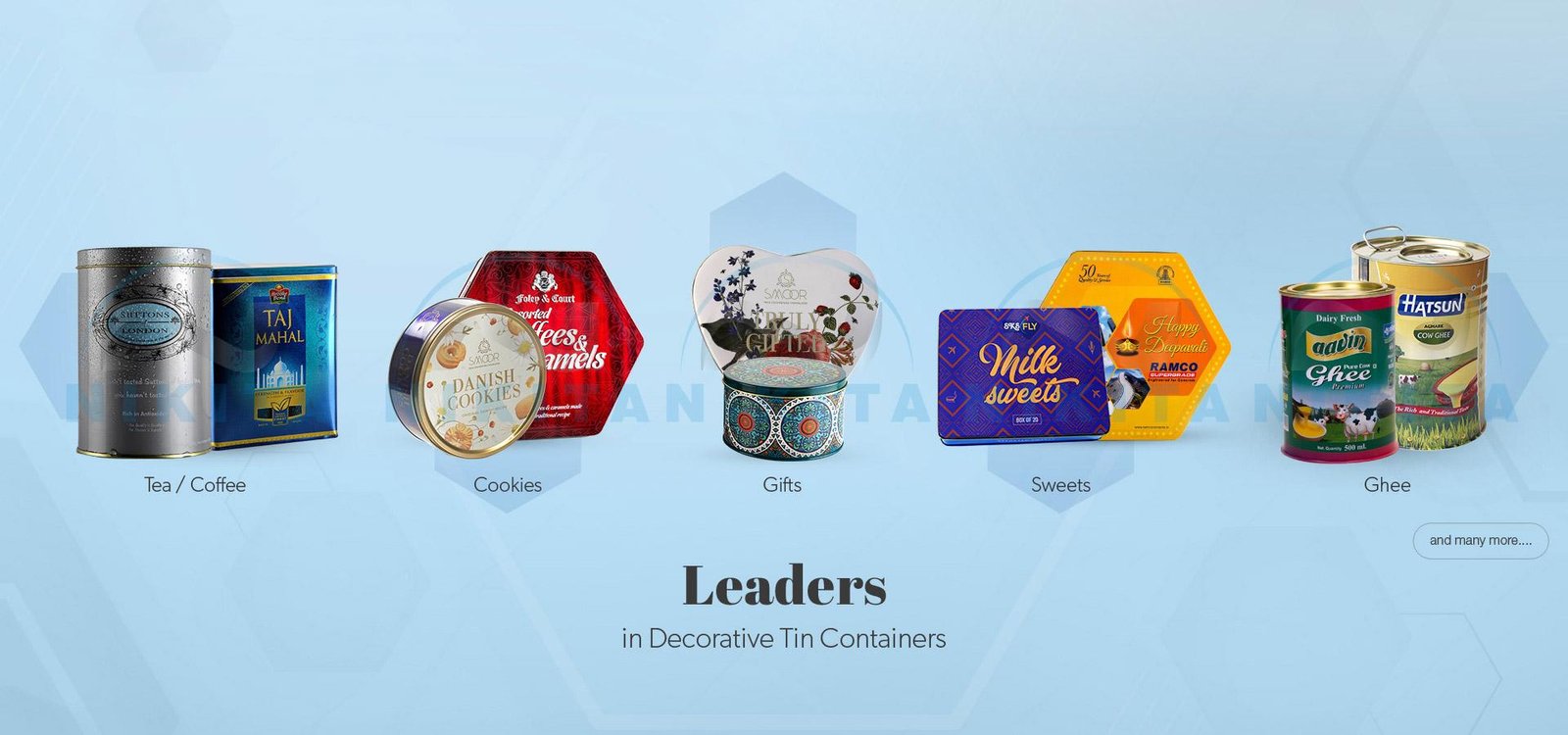
Tin boxes have become a popular packaging solution for brands across industries due to their durability, premium appeal, and eco-friendliness. But how are these high-quality containers created? The process of manufacturing tin boxes involves multiple steps, from designing and material selection to printing, shaping, and final assembly. In this blog, we explore the complete journey of tin box production, detailing each stage that ensures a perfect blend of functionality and aesthetics.
1. Concept and Design Development
The first step in tin box manufacturing begins with the design phase, where brands and manufacturers collaborate to create a packaging solution that aligns with branding and product requirements. Key aspects considered during this stage include:
- Shape and size: Whether it’s a round, rectangular, or custom-shaped tin, the structure is tailored to the product.
- Material selection: High-quality tinplate is chosen based on durability and sustainability needs.
- Branding elements: Logos, graphics, and color schemes are planned to enhance brand identity.
Modern manufacturers use advanced design software to create 3D mockups, allowing clients to visualize the final product before production begins.
2. Material Selection and Preparation
Once the design is finalized, manufacturers select the right grade of tinplate—a thin sheet of steel coated with tin for corrosion resistance. The chosen tinplate undergoes:
- Cutting into sheets based on the required box dimensions.
- Surface treatment to ensure smooth printing and prevent rusting.
- Quality inspection to eliminate any defects before printing.
3. Printing and Decoration
Printing is a crucial step in making tin boxes visually appealing. Manufacturers use various printing techniques, including:
- Lithographic (offset) printing: Provides high-resolution graphics and vibrant colors.
- UV printing: Enhances details with a glossy, durable finish.
- Embossing and debossing: Adds texture to logos and patterns.
- Matte, gloss, or metallic coatings: Enhances the overall look of the tin.
Once printed, the sheets are cured in an oven to ensure the ink adheres permanently to the tin surface.
4. Cutting and Forming the Tin Components
After printing, the tinplate sheets are cut into specific parts required to assemble the tin box. These parts typically include:
- The lid
- The body (sides of the tin)
- The base (bottom of the tin)
Machines precisely cut and shape these pieces using specialized molds to ensure consistency in size and design.
5. Shaping and Assembly
Once the tin components are cut, they are formed into their final shape through a series of steps:
- Bending and rolling: The tin body is bent and shaped into a cylindrical or rectangular form.
- Seaming and joining: The edges are welded or mechanically joined to create a secure structure.
- Lid and base attachment: The top and bottom parts are securely fitted to ensure proper closure.
This stage is crucial to achieving a well-constructed, durable tin box that provides both protection and ease of use.
6. Coating and Quality Inspection
To ensure longevity and product safety, the tins undergo a protective coating process, which may include:
- Food-grade coatings for tins used in packaging food and beverages.
- Rust-resistant finishes to improve durability.
- Scratch-resistant varnishes to maintain the tin’s visual appeal.
Each tin is then inspected for any defects, ensuring that only high-quality products move to the final stage.
7. Packaging and Distribution
Once the tin boxes pass quality control, they are carefully packed and prepared for shipment. Depending on client requirements, they may be:
- Individually wrapped for added protection.
- Stacked in bulk for efficient transportation.
- Customized with inserts or protective layers for delicate products.
The tin boxes are then shipped to businesses worldwide, ready to enhance product packaging with their premium look and durable build.
Conclusion
The manufacturing of tin boxes is a precise and detailed process, involving design, material selection, printing, shaping, and final assembly. With advances in printing, customization, and eco-friendly materials, tin packaging continues to be a preferred choice for brands looking to elevate their packaging. Understanding this process helps businesses make informed decisions when selecting a tin box manufacturer, ensuring the best combination of durability, aesthetics, and sustainability.
